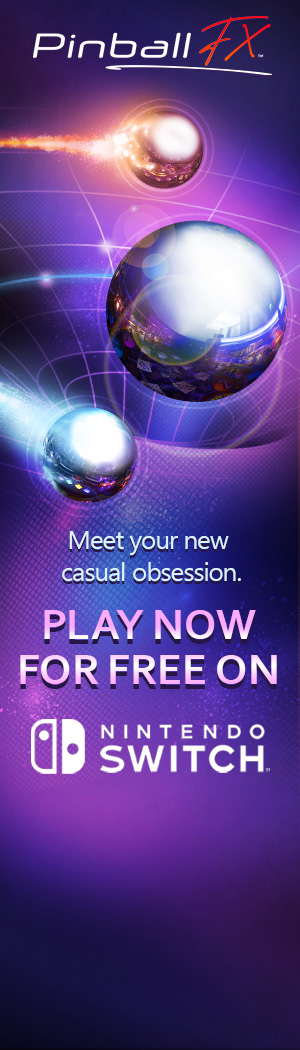
Dear Reader:
Nintendo Labo dev interview: Part 2 - A nose-picking prototype, deciding to use cardboard, and much more
- the first idea the dev team tried that lead to the creation of Nintendo Labo was a pair of scissors
- trying this idea helped the team realize that restricting the Joy-Con to enclosures helped get more accurate data
- most people found the prototypes to be a unique idea that would never get off the ground
- the original prototypes were made with a 3D printer, but plastic would end up being to pricey for the consumer
- the team involved wanted to make something unique for Switch, which is why they gathered to have “prototype parties”
- the team decided to ignore concerns about cost and just let their imaginations run wild
- the team realized that getting data from the IR Camera was a struggle due to the Joy-Con being in motion
- when then put the Joy-Con into a box and it was stabilized, the data from the IR Camera was much easier to use/read
- the first prototype the team created for the Joy-Con IR Camera project is below
- the team used a nose-picking prototype because the nostril was the smallest enclosure they could think of to test their idea
- the IR Camera inside the box responds to movement and translates it to the finger on the screen
- for the nose-picking game, the team used a 3D printer
- the team then went and collected packaging material from the storage room to make a tank prototype
- a Joy-Con is inserted in the bottom, and there are reflective balls suspended beneath the pedals that move up and down
- the tank kept breaking because the player had to put his full body weight on it
- the data from the gyro sensor wasn't being used much either when playing the tank game
- this is when the team decided to shift the whole idea to a pack you wear on your back, which lead to the Robot Kit creation
- Kawamoto had the idea that Nintendo should incorporate the “making” process into the final product
- Nintendo made a music box prototype that they didn't find fun at all
- you turned a handle at different speeds to play the music slower or quicker
- the team didn't see players enjoying this much, as the prototype really doesn't look anything like a music box
- this is where the team learned the importance providing the whole experience to the consumer
- this lead to the idea of using cardboard to let the consumer create the device they would then play with
- all these ideas of customization and building also lead to the idea of the Toy-Con Garage mode
- after the first prototype, the hardware department were thinking of ways that they could put the IR Motion Camera to use
- the hardware team came up with their own prototypes at this point, including an “optical attachment”
- this prototype had reflective tape affixed to it to serve as a marker
- the Joy-Con emits a beam of invisible infrared light that is reflected back by these markers
- this enables the camera to read their movement
- this lead to a fishing rod prototype
- after this, a giant controller out of cardboard was made and was called the “Big-Con”
- you could push the big buttons, and that would move a reflective marker up and down inside the box
- the IR camera would read the motion of the markers
- the hardware team also independently started thinking that cardboard was the way to go for this project
- the hardware and software teams joined forces to share ideas shortly thereafter
- there were a lot of people on the software prototyping team that happened to really enjoy arts and crafts
- their interests ended up influencing the final product
- the initial prototype brainstorming sessions lasted about three weeks
- the team had a lot of prototypes that they pushed aside as they didn't find them to be fun
- the Toy-Con Motorbike designer was previously responsible for overseeing the Nintendo Switch and Joy-Con hardware
- the Nintendo Switch stand designer ended up designing the Toy-Con Piano
- the Nintendo Switch Pro Controller designer worked on another Toy-Con
- the two software art directors for Nintendo Labo worked on The Legend of Zelda and Animal Crossing
- a group of programmers showed the dev team their Toy-Con RC Car auto-driving mode, which they figured out on their own
- Nintendo considered the durability of the materials during the design stage
- they designed the Toy-Con projects so that they wouldn’t break easily
- the team performed extensive durability tests where they were subjected to the same motions and actions thousands of times
- cardboard is typically made from recycled paper, and the recycling process gives a final product with all kinds of materials
- North America, Europe, and Japan produce cardboard sheets for their region to comply with regional requirements
- the more the team worked on their creations, the more they wanted to customize them and give them their own sense of style
- the software includes tips on how to make repairs
- there are videos in the Discover section explaining how best to repair certain things, and how to avoid mistakes
- there is also content on decorating tips, and how to reinforce completed Toy-Con projects
- there are videos on how to replace snapped rubber bands, and how to use masking tape to repair cardboard tears
- there were consumer tests to see how difficult building certain Toy-Con was
- when something came across as too difficult for a child, the team took it back into the workshop and redesigned it
- at the Nintendo Labo preview events, lots of kids ignored the scheduled break times in order to play/build more
- the Robot Toy-Con takes three or four hours to build,
- speaking generally, children six and up can probably handle Nintendo Labo projects with a little assistance from their parents
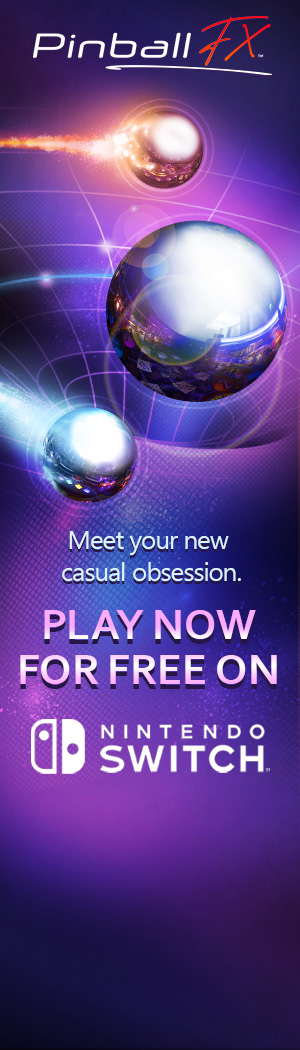